What is Porosity in Welding: Trick Variables and Their Influence On Weld High Quality
What is Porosity in Welding: Trick Variables and Their Influence On Weld High Quality
Blog Article
Porosity in Welding: Identifying Common Issues and Implementing Finest Practices for Prevention
Porosity in welding is a pervasive issue that frequently goes unnoticed till it triggers significant issues with the honesty of welds. In this discussion, we will discover the vital variables adding to porosity development, analyze its damaging effects on weld performance, and go over the ideal methods that can be taken on to decrease porosity occurrence in welding procedures.
Usual Reasons of Porosity
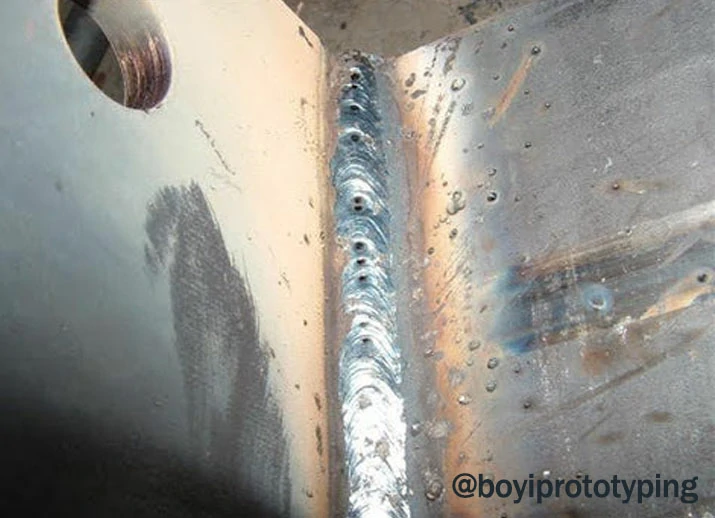
Utilizing dirty or damp filler products can introduce pollutants into the weld, adding to porosity concerns. To alleviate these typical reasons of porosity, complete cleaning of base steels, proper securing gas selection, and adherence to optimal welding criteria are essential practices in attaining premium, porosity-free welds.
Influence of Porosity on Weld Top Quality

The visibility of porosity in welding can substantially jeopardize the structural stability and mechanical properties of bonded joints. Porosity produces voids within the weld metal, weakening its overall toughness and load-bearing capability.
Welds with high porosity degrees often tend to exhibit lower effect strength and minimized capacity to flaw plastically before fracturing. Porosity can impede the weld's ability to properly transfer forces, leading to premature weld failing and potential safety hazards in crucial structures.
Ideal Practices for Porosity Prevention
To boost the architectural integrity and high quality of welded joints, what particular procedures can be carried out to lessen the event of porosity throughout the welding process? Porosity prevention in welding is important to guarantee the stability and stamina of the last weld. One reliable technique is proper cleaning of the base steel, eliminating any impurities such as rust, oil, paint, or dampness that can lead to gas entrapment. Making certain that the welding devices is in great condition, with tidy consumables and suitable gas flow prices, can also significantly minimize porosity. Additionally, keeping a stable arc and regulating the welding criteria, such as voltage, present, and take a trip rate, assists produce a regular weld swimming pool that reduces the danger of gas entrapment. Making use of the proper welding method for the particular product being bonded, such as changing the welding angle and gun placement, can further avoid porosity. Normal inspection of welds and instant removal of any issues identified during the welding procedure are crucial techniques to avoid porosity and create top notch welds.
Value of Correct Welding Techniques
Carrying out proper welding strategies is paramount in ensuring the architectural honesty and top quality of bonded joints, constructing upon the foundation of efficient porosity prevention measures. Too much heat can lead to enhanced porosity due to the entrapment of gases in the weld pool. In addition, making use of the ideal welding specifications, such as voltage, current, and travel speed, is important for accomplishing audio welds with minimal porosity.
Moreover, the choice of welding process, whether it be MIG, TIG, or stick welding, ought to align with the specific requirements of the job to ensure optimum results. Appropriate cleaning and preparation of the base metal, in addition to selecting the ideal filler material, are also important elements of competent welding techniques. By adhering to these ideal look at this now techniques, welders can minimize the threat of porosity development and create top quality, structurally sound welds.
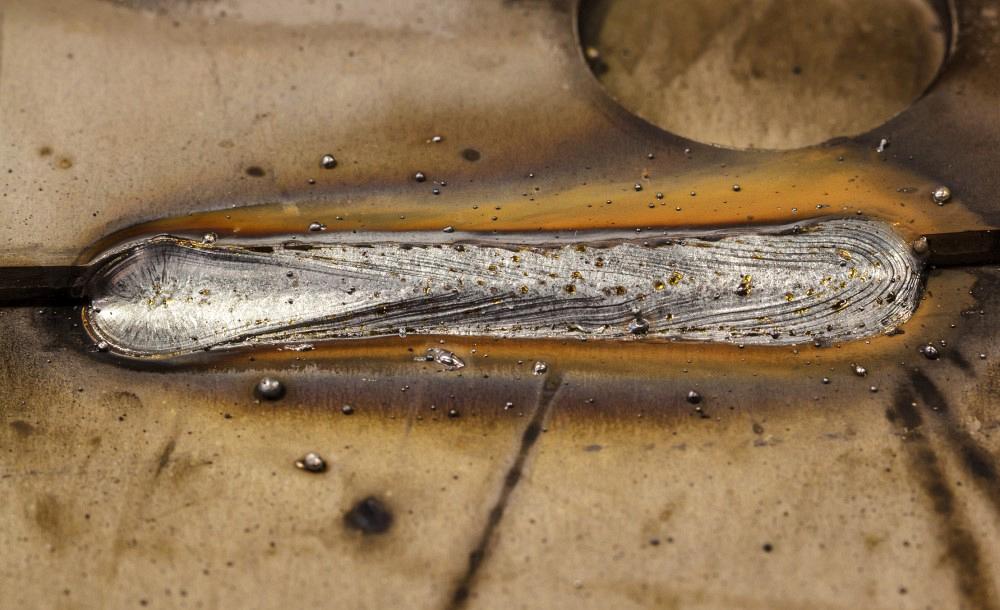
Testing and Quality Assurance Steps
Quality assurance steps play a vital function in verifying the integrity and dependability of bonded joints. Testing procedures are necessary to identify and prevent porosity in welding, ensuring the stamina and durability of the end product. Non-destructive screening approaches such as ultrasonic screening, radiographic testing, and aesthetic assessment check this are commonly utilized to recognize possible flaws like porosity. These strategies permit the assessment of weld high quality without jeopardizing the honesty of the joint. What is Porosity.
Conducting pre-weld and post-weld examinations is also important in maintaining quality control standards. Pre-weld evaluations include verifying the products, tools setups, and cleanliness of the work location to stop contamination. Post-weld evaluations, on the various other hand, evaluate the last weld for any type of issues, including porosity, and verify that it fulfills defined requirements. Carrying out a detailed quality assurance plan that includes thorough testing treatments and assessments is extremely important to minimizing porosity issues and making certain the general top quality of welded joints.
Final Thought
To conclude, porosity in welding can be a typical problem that impacts the high quality of welds. By recognizing the typical sources of porosity and try these out applying ideal practices for avoidance, such as proper welding techniques and screening steps, welders can ensure high quality and reliable welds. It is important to prioritize avoidance techniques to lessen the incident of porosity and keep the integrity of bonded structures.
Report this page